Why Optimise Inventory?
Inventory is not an asset; it is a liability and a risk.
According to Sam Smale, fellow at Cranfield University, the cost of holding inventory ranges from 15% to 45% per annum and is made up of the capital, obsolescence, storage, handling, spoilage, pilferage, damage and insurance costs. Less obvious is the issue of time. Eight weeks of stock in a supply chain means eight weeks before you can introduce a replacement product.
Therefore, if we are conservative and assume a stock holding cost of just 15% per annum, for every £1,000,000 of inventory that is taken out of the supply chain, a company saves £150,000 per annum. Another issue to consider is the lost revenue resulting from stock-outs or shortages. This is harder to quantify but often has a greater impact on the bottom-line of a business. A further concern is the creation of waste due to surplus inventory of perishable or short life-cycle products.
Inventory Holding Costs
Capital | 8% - 25% |
Obsolescence | 1% - 5% |
Storage and Handling | 2% - 6% |
Spoilage, Pilferage and Damage | 3% - 10% |
Insurance | 1% - 4% |
Total | 15% - 45% |
Inventory Optimisation Solutions from ValueMetrics
An Engineered Approach
Inventory Optimisation with ValueMetrics is, first and foremost, a best practice methodology matured through years of experience leading inventory management and supply chain design projects with the pioneers of the field in Europe, USA and Africa. For us the objective of Inventory Optimisation is quite simple - to sustain minimal amounts of inventory while providing the highest possible service levels. The ValueMetrics Inventory Management Methodology is based on our belief that the right approach is through the engineering of the planning process, while supporting it with a state-of-the-art Inventory Optimisation software system to ensure that you have the right stock in the right place at the right time.
State-of-the-Art Inventory Optimisation Software
By deploying our Inventory Management Methodology, supported by a state-of-the-art Inventory Optimisation software system we assist you to determine the optimal levels of inventory for your business, which can lead to significant inventory reductions. The software system is widely regarded by analysts as not only the most sophisticated, but also highly effective inventory management software available. The solution is designed as a management tool and not a transaction-based system. Its functionality is very comprehensive and is structured to focus the user’s attention on the areas that will yield the greatest improvements in the shortest possible time. Our solution also provides a level of intelligence and flexibility that is not available in ERP systems.
Multiplatform Integration Across Extended Supply Chain
The software system is highly adaptable and able to interface with your business systems and those of your suppliers and customers. The unique architecture of the software supports the continuous flow of information from any ERP or in-house systems across many sites to optimise the value of existing infrastructure and data.
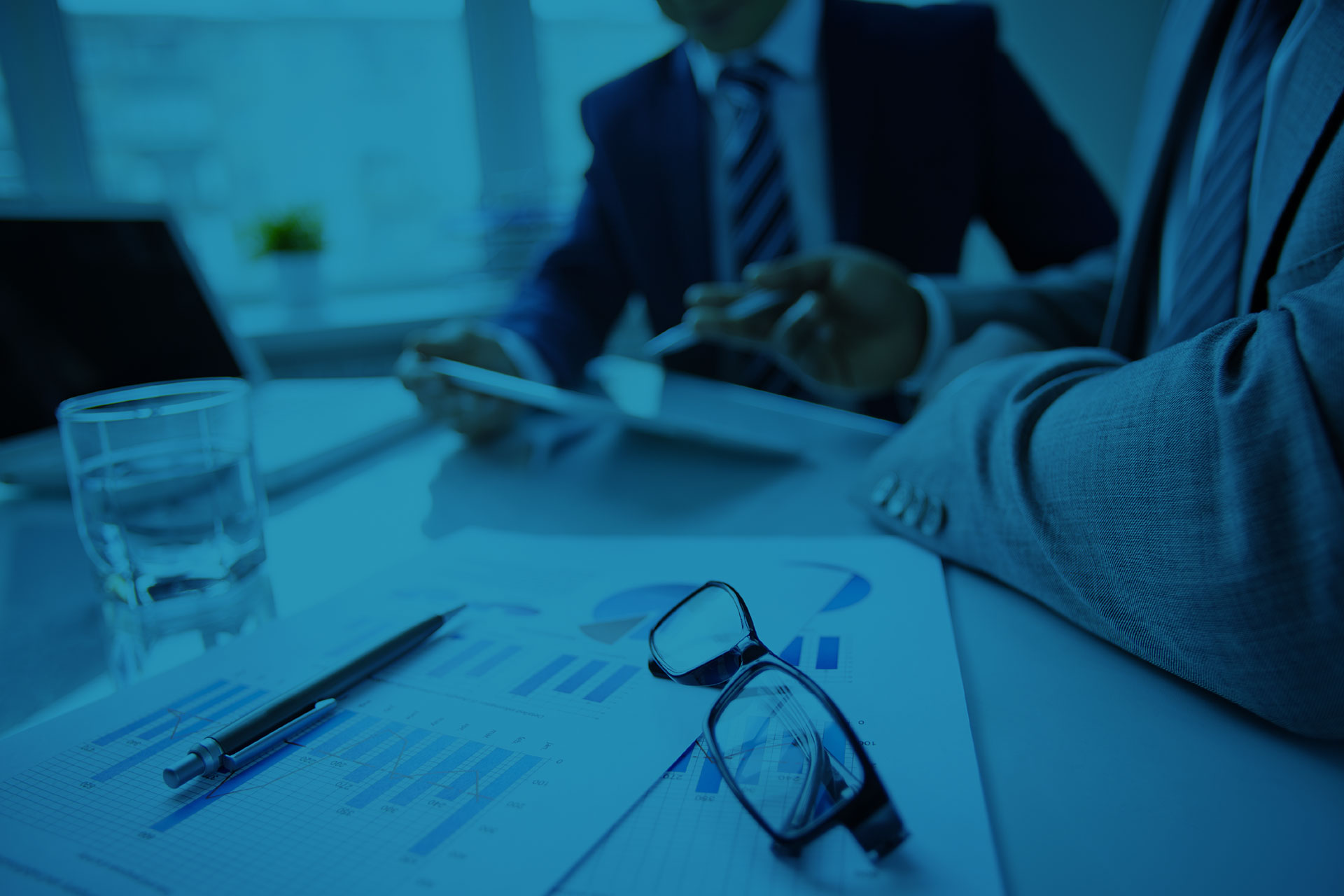
Our Approach
ValueMetrics Inventory Management Methodology
We have honed our Inventory Management Methodology over decades of implementing many inventory optimisation programs spanning a wide range of industries across Europe, USA and Africa. At ValueMetrics experience has taught us how to implement an effective inventory management process, underpinned by the right inventory management software, and that is supported by well-trained people, thereby ensuring that results are sustained.
ValueMetrics’ Inventory Management Methodology through appropriate best business practices in inventory and replenishment planning delivers business benefits simultaneously, along two lines:
- Revenue improvement through increased customer service levels that directly impact the top line;
- Costs reduction through optimised inventories and reduced working capital that directly impact the bottom line.
The ValueMetrics Inventory Management Methodology delivers these benefits through:
Process Enhancement - with low risk and low organisational impact
- Best practice
- Process automation
- Improved performance monitoring
- Maintained timely corrective action
Efficiency
- Working capital cost reduction through optimised inventory
- Reduced inventory write-offs and write-downs
- Operating costs reduction such as warehousing, handling, expediting, etc.
Performance
- Improved availability which leads to improved customer service levels
- Reduced stock-outs and lost sales
ValueMetrics’ Inventory Optimisation Solutions are flexible, simple to use, easy to understand, and cover the key elements of Inventory Management:
- Supplier and Lead Time Management
- Stock Profiling and Classification
- Forecast and Demand Planning
- Inventory Modelling and Strategic Planning
- Replenishment and Distribution
- Key Performance and Process Monitoring
Why choose ValueMetrics Inventory Optimisation Solutions?
ValueMetrics’ Inventory Optimisation software system is developed by the leading minds in Demand Planning, Inventory Optimisation and Supply Chain Planning, and it offers the world’s best and most sophisticated technology capabilities in these fields. This technology underpinned by the ValueMetrics Inventory Management Methodology can deliver inventory reductions between 15% and 50%, and/or service level improvements of up to 20% (or higher, depending upon current levels). These are realistic improvement targets, frequently achieved by companies that have implemented similar solutions.
Resulting Savings of ValueMetrics Inventory Optimisation Solutions
Inventory reduction
50%Service level improvement
20%Improved inventory availability
15%What Could a ValueMetrics Inventory Optimisation Solution Do for You?
The fundamental problem that exists in most businesses today is that there is no link between the level at which top management sets corporate inventory holding polices and the level at which line items are ordered. Having the ability to quickly and easily model the effect of different inventory holding policies on the inventory and service levels of a business is imperative in today’s competitive business environment.
Significant Reduction in Working Capital
The ValueMetrics Inventory Management Methodology supported by our Inventory Optimisation software system enables us to effectively determine the optimal levels of inventory for your business, typically leading to significant inventory reductions.
Unique to Your Business
ValueMetrics deliver Inventory Optimisation Solutions that will help your company to build an inventory model of your business that takes into account the unique supply and demand characteristics of your supply chain. Based upon demand forecasts, customer orders, supplier lead times, user defined replenishment rules, current stock levels and the existing order pipeline, we provide Inventory Solutions that will calculate the ideal levels of safety stock for every line item at every level in your supply chain.
Rapid and Sustainable Results
Having completed many inventory optimisation programs across a wide range of industries, ValueMetrics has gained significant experience how to implement an effective inventory management process for you that is supported by well-trained people thereby ensuring that results are sustained. Our sophisticated inventory software tools are also designed to achieve the maximum improvement to your supply chain in the shortest possible time.
Service Level Improvement
Our customers not only experience significant inventory reduction through a ValueMetrics Inventory Optimisation Solution, but also a sustainable service level improvement. Order management is the process that converts demand, inventory availability and inventory policy into the required replenishment orders. Not only does the ValueMetrics Inventory Management Methodology ensure that every new replenishment order is in line with the inventory holding objectives of your business, but it is also constantly, and pro-actively, review the order pipeline, suggesting actions that will ensure that you optimise your investment in inventory and deliver high levels of availability to your customers.
Reducing Excess Stock, Increasing Cash on Hand
Whilst the ValueMetrics Inventory Management Methodology will ensure that you minimise the creation of excess stock, unanticipated changes in the market may result in excess inventory. The methodology provides for the disciplines and approaches to proactively identify excess stock and surplus orders and monitor the effectiveness of excess stock action plans. The software system allows you to identify excess stock items quickly.
We design and implement Inventory Optimisation Solutions that are focussed on delivering optimised inventory holding and increased customer service levels.
The benefits of a ValueMetrics Inventory Optimisation Solution are:
- The establishment of realistic investment and availability objectives
- Improved forecasting accuracy
- Improved inventory availability
- Reduced inventory holding
- Reduced lost sales and improved customer satisfaction
- Reduced waste
- Reduced emergency orders and changes to order schedules
- Reduced obsolescence
- Reduced inventory write-offs and write-downs
- Rationalised product range
- Improved staff motivation, productivity and job satisfaction
- Better visibility of inventories
- Uniform inventory management processes across organisations
- A higher degree of automation of the demand to replenishment process